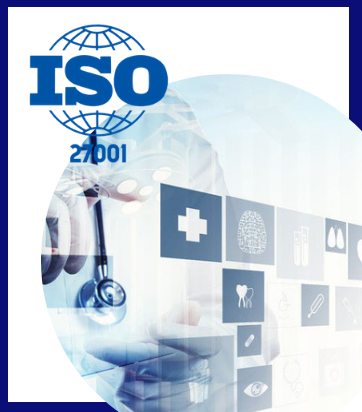
A course on ISO 27001:2013 Standard
What is information security? It ensures the privacy of your information with the ISO/IEC 27001 certified system and demonstrates that you can control inform...
Originating from the phyloshophy that human development is putting human at the centre, 5S model has been widely implemented in Japan as a foundation for quality management system. 5S helps create a clean, confortable working environment, facilitate the adoption of quality management system, thereby build customer’s trust.
5S is a tool to improve quality performance originating from Japan. Its name comes from S letters in Japanese including:
Seiri, Seiton, Seiso, Sheiketsu và Shitsuke which can be translated into as "Sort", "Set In order", "Shine", "Standardize" and "Sustain"
1. Sort – S1 (Seiri):
Check everything to determine which is nececessary for production and which is not, then remove unnecessary items as soon as possible. Only essential stuffs are allowed to be present at working location. S1 is often conducted preodically.
2. Set in order – S2 (Seiton):
“Set in order” means arranging stuffs, semi-finished products, material, goods etc in convenient and recognizable location. General rule is that any stuff has its own place with clear identification mark. This activitiy need strictly following.
3. Shine – S3 (Seiso):
Shine is understood as keeping working place, tool and surroundings clean and hygienic. S3 is also implemented regularly.
Standardize means maintaining the the repetition of processes used to sort, order and clean the workplace. To ensure the continuation of 3S, thay can set out regulation specifying 3S responsibility, method and frequency of individuals.
5. Sustain – S5 (Shitsuke):
Sustain is demonstrated through self-discipline of labor in 5S. Each individual needs to be full aware of the importance of 5S, self-aware and active in implementing 5S. Therereby, their working performance coulb be improved considerably.
Items |
Days/Experts |
Differences |
Topic |
01 S1- S2- Types of waste Lean |
03/ |
Not simple as "Sort", "Set In order", "Shine", "Standardize" and "Sustain". In Lean’s option, 5S means remove waste and illogicality to improve productivity and quality, safe working environment and creativity. Thus, the program is designed to integrate with Lean and other advanced tools. |
- Training on 5S và Eleminating waste (Lean) - Training on building a 5S organizational structure - A guide to scene inspectation - Audit on current situation 1ST (experts and steering board) - Make plans for (S1) remove unnecessary items and plan (S2) arrangements - A guide to draw layout and label resource for each area. - A guide to design banner, poster - Decisions on launching 5S champagne Note: Company prepares classroom, board, pens, A1 paper, camera; assign participants ( including a member board of director) |
02 S1- S2 |
0 |
|
- Propaganda - communication about the program - Visualize instructed information. - Perform screening for 1st time (points detected by the expert's recommendation) unnecessary objects - Iplement schedualed arrangement Note:The 5S Steering Board monitors the implementation and weekly reports progress to the Board of Directors and Professionals. The Specialist is always closely supervising the operation and off site support during implementation. |
03 S1- S2- S3- 3R-
TPM and 6 Loss Kaizen |
03/ |
When deploying 5S purely, the S3-Shine will be interpreted as cleaning, Actually, it is not simple like that: Activities in S3 must be closely linked to the analysis and identification of potential abnormalities Thus, the program is designed in line with a comprehensive Productivity Maintenance (TPM) approach that identifies and eliminates six types of machinery and equipment losses. Accompanying this is the launch of the Kaizen program by setting up taskforce teams to maintain and continually improve the 5S program in the future and help the company access other advanced methods and tools. (eg Lean6sigma ...) |
- Check practice of screening and arrangement, guide to adjust properly. - A guide to standardize S1 and S2 - Training on issue detecting and solving skills - 5S – 3R Activities - Training on 5S-TPM and 6 types of the most serious damage toward machne/ equipment - A guide to set up a special task team and choose improvement theme (Kaizen) - A guide to implement S3 và make plan for S4 Note: The 5S steering board collaborates with train to check implementation and pre-audit of company. |
04 S1- S2- S3 |
0 |
|
- Special task groups following the recommendations of the train in section 03 Note: The 5S steering board supervises the implementation and reports the weekly progress to the Board of Directors and the Expert |
05 S1- S2- S3- S4 SS QCC |
02/ |
For traditional 5S, maintance can not be continued due to not deliver maintaince method. Therefore, the program is designed to maintain and continually improve the 5S system by: The innovative system (SS) and inter-agency (QCC) In order to do this, the company must develop and standardize its activities and set higher goals for each period. In addition, there must be a system of accreditation, certification, recognition and encouragement. |
- A guide to make audit sheet - 2nd Audit (experts and group) - Training on assessing skill 5S auditor - Training on buiding improvement suggestion system (Suggestion system – Quality Cycle) Note: The 5S steering board collaborates with training to check implementation |
06 S1- S2- S3- S4
|
0 |
|
-The units perform corrective for the inappropriate points in the second audit - The groups self-assess their area and report the first, second, and third week (in 3 weeks) - Handbook 5S (application guide) - Task Group (Kaizen) Note: The 5S Steering Board supervises the implementation and reports the weekly progress to the Board of Directors and the Experts |
07 S1- S2- S3- S4 |
01/ |
Beside training, we also collaborate with company to issue internal certificate for members who complete practice period and knowledge examination We spend a lot of time auditing and reminding position and areas to well practice of standard
|
- 3rd 5S audit lần III (Experts and group), take photos of 5S implementation and compare - Instruct and adjust current situation, file, document - Check and test position Note : The 5S steering board collaborates with training to check implementation |
08 S1- S2- S3- S4- S5 |
|
|
-The units perform corrective for the inappropriate points in the second audit - The groups self-assess their area and report the first, second, and third week (in 3 weeks) - Edit handbook 5S (guide to implement) - Special task group make progress report l (Kaizen) - Chuẩn bị báo cáo sơ kết việc thực hiện 5S tại đơn vị. - Chuẩn bị bằng chứng nhận cho các thành viên đạt 5S Note:The 5S Steering Board supervises the implementation and reports the weekly progress to the Board of Directors and the Experts |
09 S1- S2- S3- S4- S5- Kaizen |
01/ |
We focus on creating group environment and continuously improvement culture for company Besides, we given some instruction in 5S handbook for anyone to read and understand their role and task in 5S We help enhance ability and soft skills for group leaders through instructing them methods and essential tools |
- 4th audit of the implementation of 5S, review report on the implementation of 5S in units - Instruct the Kaizen project team - Guide to make preliminary report on 5S implementation at company Note: The 5S Steering board works with training to evaluate the implementation and validation of the products |
10 |
|
We use professional and specified form for specific area in order to learn and continuously improve |
- The groups / units complete the items - Develop OPL (one point lesson) - Issue 5S Manual Note: The 5S Steering Board supervises the implementation and submits the reports to the Board of Directors and training. |
11 S1- S2- S3- S4- S5- Kaizen |
01/ |
Help the company maintain effective 5S operations, accompanied by a cross-sectoral / departmental assessment system In addition to the 5S, the company also has systems running in parallel: Suggestion system (SS) Quality Control Circle( Kaizen) Getting started for TPM operations Improvement culture and staff capacity changes more positively |
- Preliminary report on the 5S implementation at the Company, - Task teams report the theme and OPL - Award 5S certification for members - Encourage motivation and reward - Check the project and proposing the next plan. |
5S Objectives