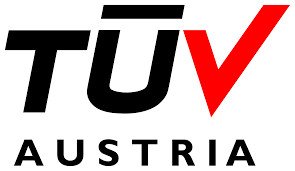
KNA COOPERATED WITH TUV AUSTRIA HELLAS ON AUDITING FSC STANDARDS IN VIETNAM
After time of exchanging and discussing, KNA CERT has successfully signed a cooperation agreement with TUV Austria on FSC/CoC certification services. Accordingl...
Definition of FMEA? Which benefit of the implementation of FMEA in production management? As we all know, 5 core tools of ISO 16949 consists of: SPC, FMEA, PPAP, APQP, MSA. Most of these tools focuses on ''the output result of process". However, FMEA is a tool which concentrates on identifying and assessing the process's consequences and potential risks, which helps to offer effective solutions to avoid its risks. In other words, this tool helps quality management system to reduce risks.
WHAT IS FMEA?
FMEA method is created to ensure that potential problems was considered and addressed during product development and process. Then, solutions are proposed to prevent these issues from occuring.
FMEA stands for Failure Mode and Effects Analysis, we will each word to perfectly understand its meaning.
Failure:
Failure is a thing no one wants to exist. Failure is the consequence of process. Nevertheless, failure emphasized in FMEA belongs to potential failure, which means that it has not occured yet but can happen in the foreseeable future failure.
Mode:
The definitions of failure mode and defect easily cause some confusion while they are different concepts. Failure emphasizes mechanism, causes while defect stresses things, the quantity of wastes.
Effects:
Effects means impacts of failure on output products. For example, a product which has a scratch on semi-finished products is only a bonded error. However, if this occurs on the packaging, inner products might be out of order.
Analysis:
This means that we have to find out causes, analyze risks and consequences, then classify and produce further improvement.
Specifically:
Exactly, FMEA is: "Analyse types of errors or ways of producing wastes and its influences on finished products or the output of process, then undertake the assessment, arrangement and take priorities over these errors' remedy".
2. Analyse types of FMEA and solutions to other problems.
Questions can be put here, which is the difference between analyzing of types of errors( Failure mode ) in FMEA and analyzing errors in problem-solving methods such as A4, 8D, 5Why, KT, Fishborn... The difference is only "time".
For FMEA:
The main activity is that we have to focus on potential errors which have not occured yet, so the biggest advantage of FMEA is timeliness, which means that we have to avoid these errors.
In other words, this problem has not occured yet so we have much time to create FMEA for all processes, products.
For problem-solving methods:
Time is very luxurious, when having a problem, pressure to stop production, pressure to release goods, pressure to cancel goods so the expense rises. Customers, the supply chain and the boss urge producers to release goods ...Therefore, FMEA analysis is not effective. While analysis methods such as A4, 8D, KT, FTA are more effective because they make careful steps to tackle problems then discover their causes. Actually, FMEA used by Vietnamese people for a long time is very simple. Please observe an example to prove these methods at the following posts: